Production
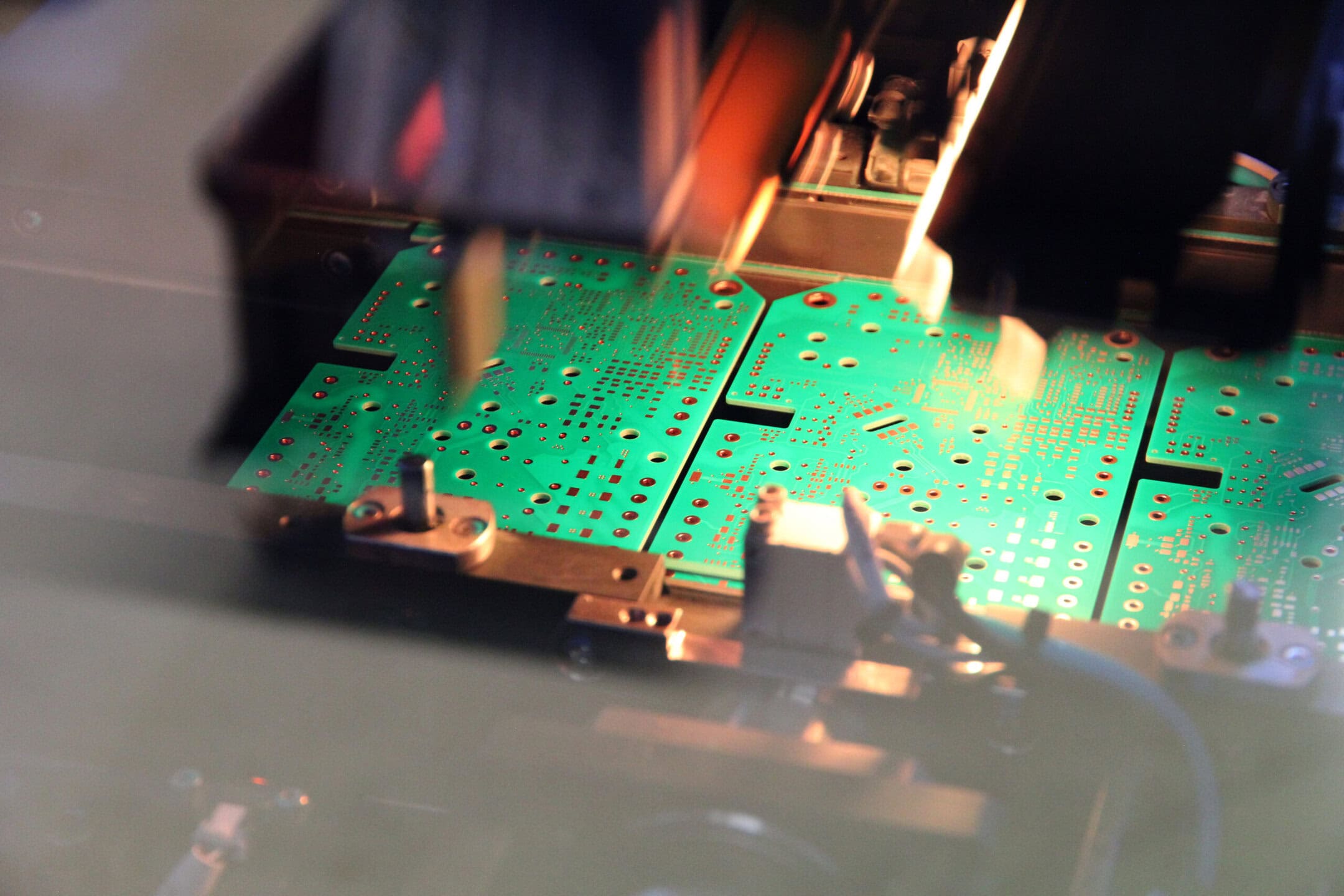
Laser marking
We use laser marking both for labelling printed circuit boards as the basis for end-to-end traceability and for labelling manufactured products with all the necessary information. A major advantage of this method is its sustainability, as it makes the use of stickers superfluous.
SMT production
Our high-performance Fuji and Samsung surface-mount technology (SMT) lines enable us to process PCBs with thicknesses from 0.5 mm to 2.4 mm and to assemble all standard component shapes. We apply adhesive and solder paste using both stencil printing and jet dispensers.
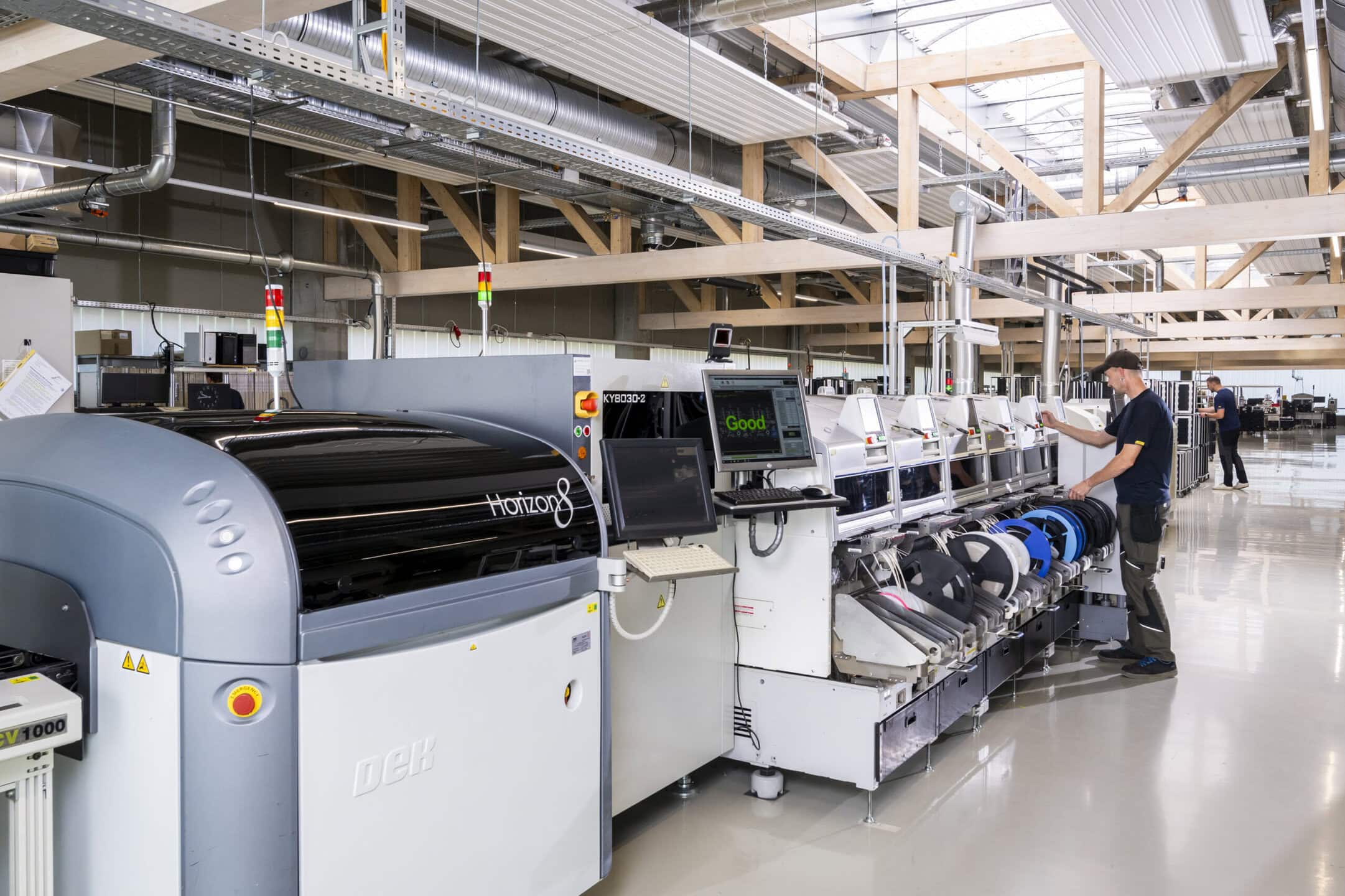
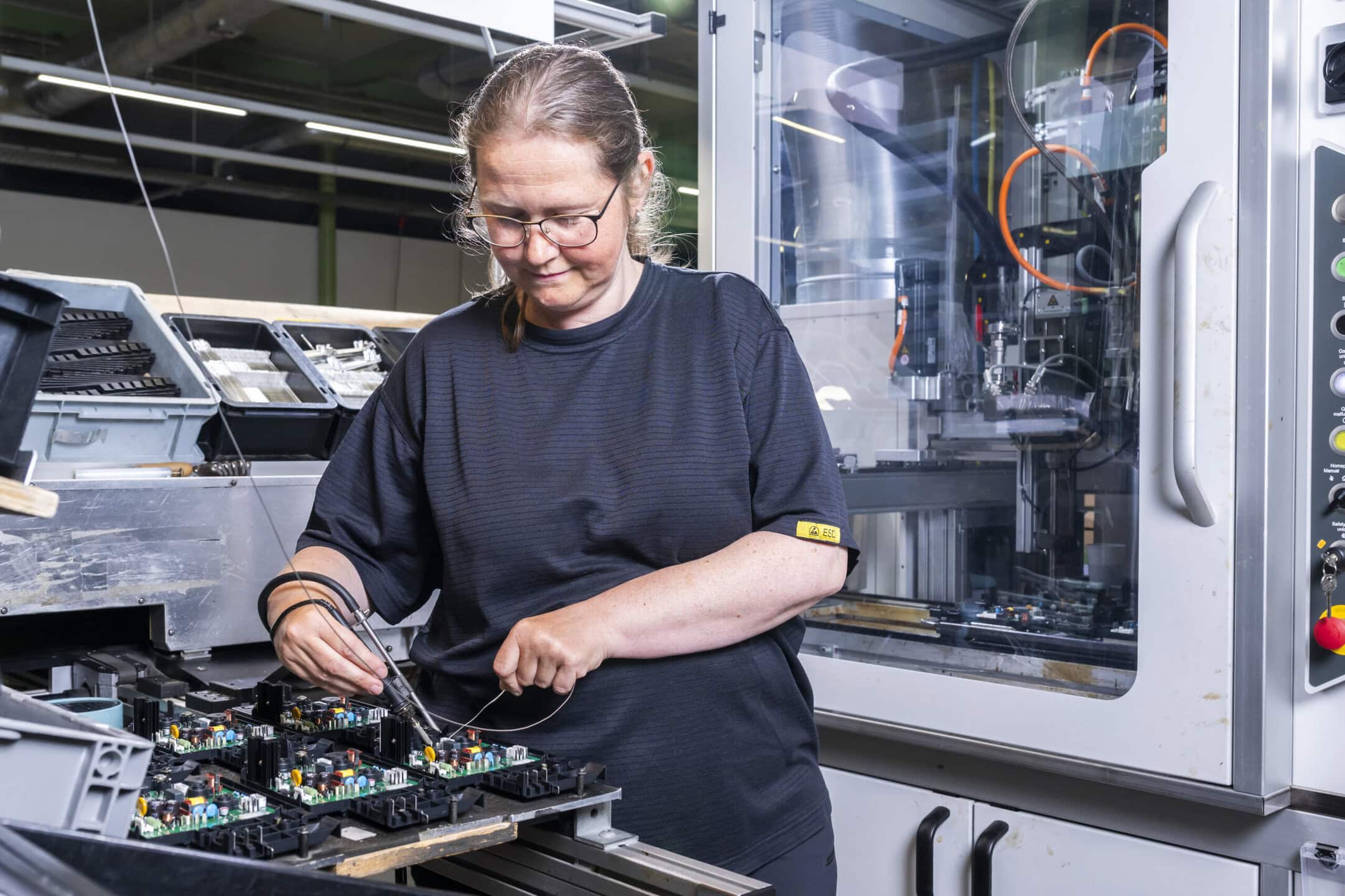
THT production
TCE has a universal assembly line for axially and radially taped components. An automatic machine for placing flat connectors of various sizes completes the portfolio. We also offer the option of classic manual assembly with subsequent wave or selective soldering. Our range of services also includes the specific preprocessing of components, such as component assembly.
Soldering technology
We fulfil our customers’ requirements for RoHS-compliant products with lead-free soldering processes throughout. Depending on the respective production technology, the following soldering processes are used:
- Reflow soldering with ovens from Ersa and Seho (SMT production)
- Wave and selective soldering with Ersa systems (THT production)
- Hand soldering
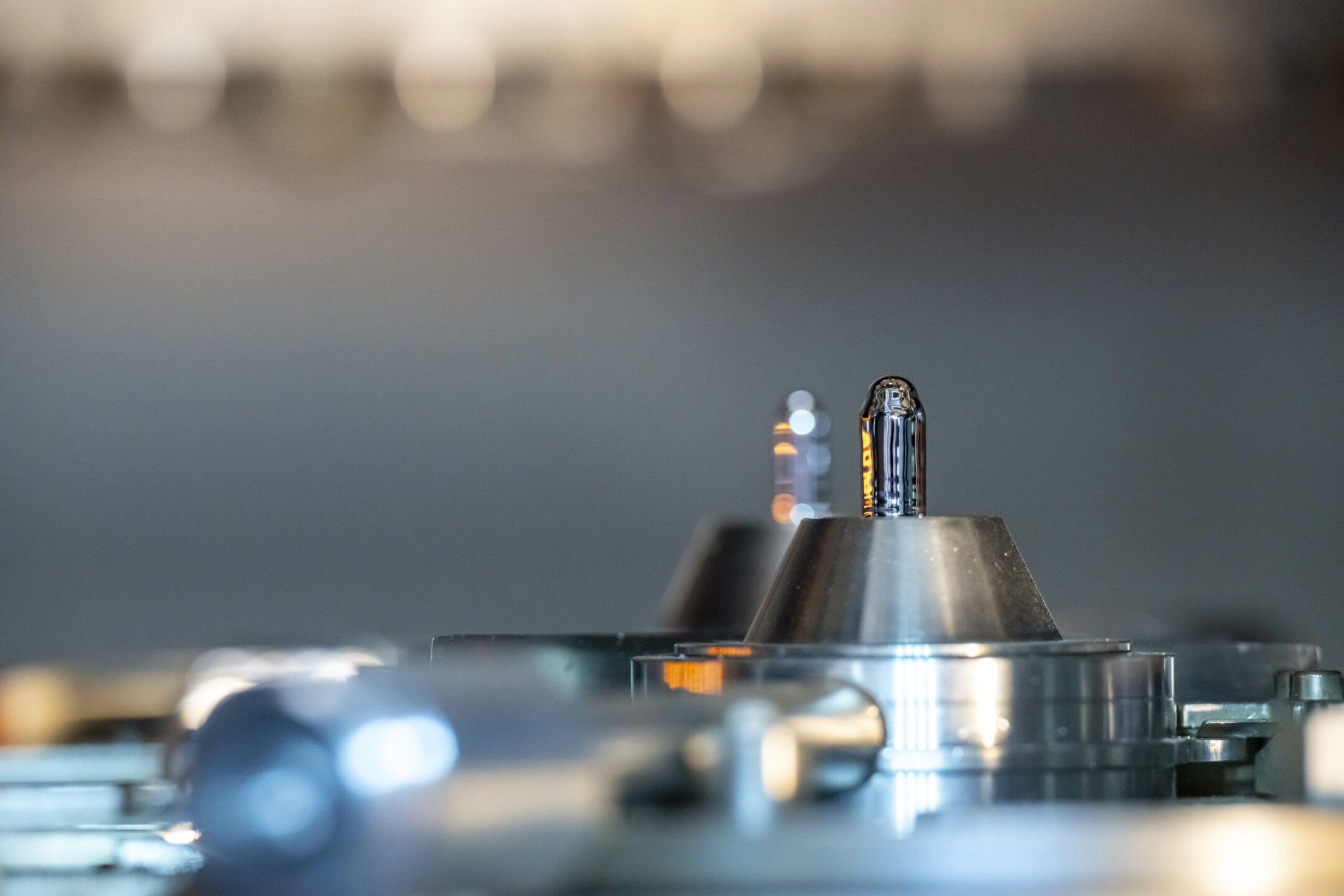
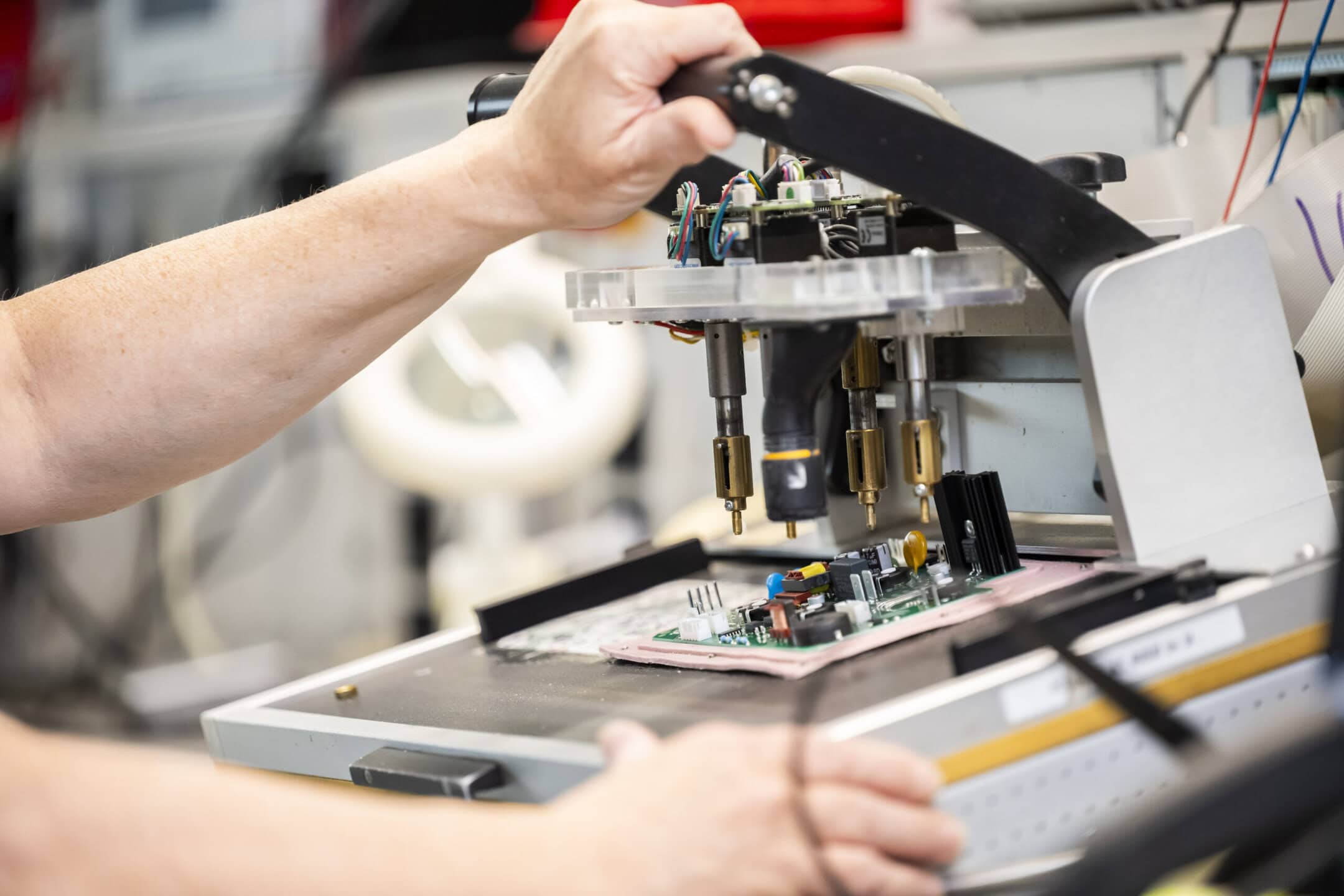
Test and inspection technology
In order to guarantee our customers products of the highest quality, functioning and safety, TCE utilises a wide range of testing and inspection technologies. We are able to develop individual test systems in-house or realise them according to customer specifications.
We utilise a wide range of testing technologies:
- Solder Paste Inspection (SPI)
- Automatic Optical Inspection (AOI)
- Testing with needle bed adapters (using vacuum needle bed adapters or automatic test cells), enabling in-circuit testing, measurement, alignment, programming and functional testing of the circuit board
- High-voltage and protective-conductor testing
- Partially and fully automated final test systems for functional testing
Painting and moulding
For painting, we use fully automatic painting machines with UV-curing thick-film paint. In contrast to thin-film coating, this process not only protects the components from moisture, but also from mechanical damage.
With our fully automatic potting lines from Scheugenpflug, we are able to realise two-component potting under constant conditions (material preparation under vacuum, with temperature control and agitator) and thus achieve a consistently high potting quality. A vacuum potting system is available for special applications.
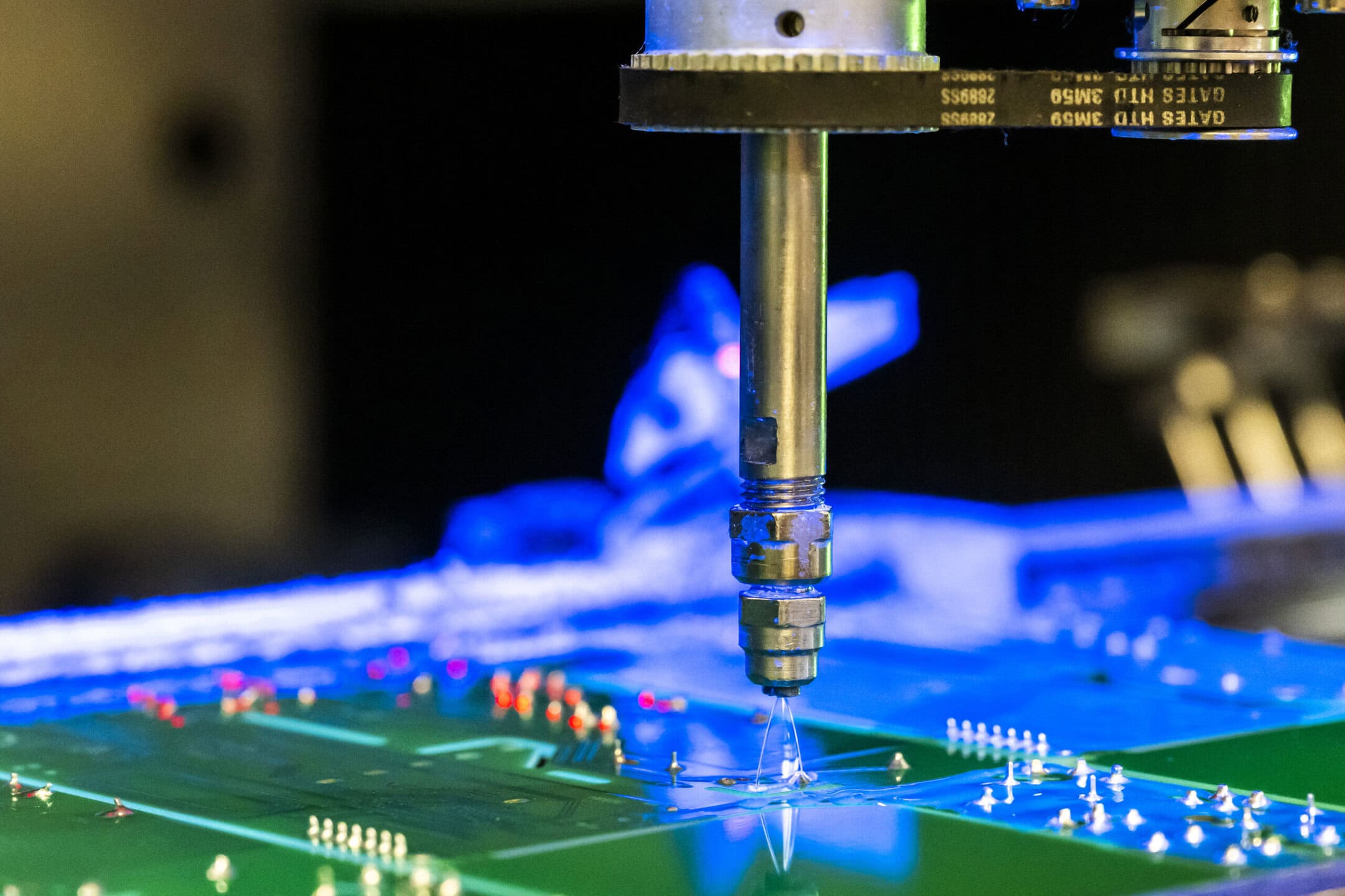
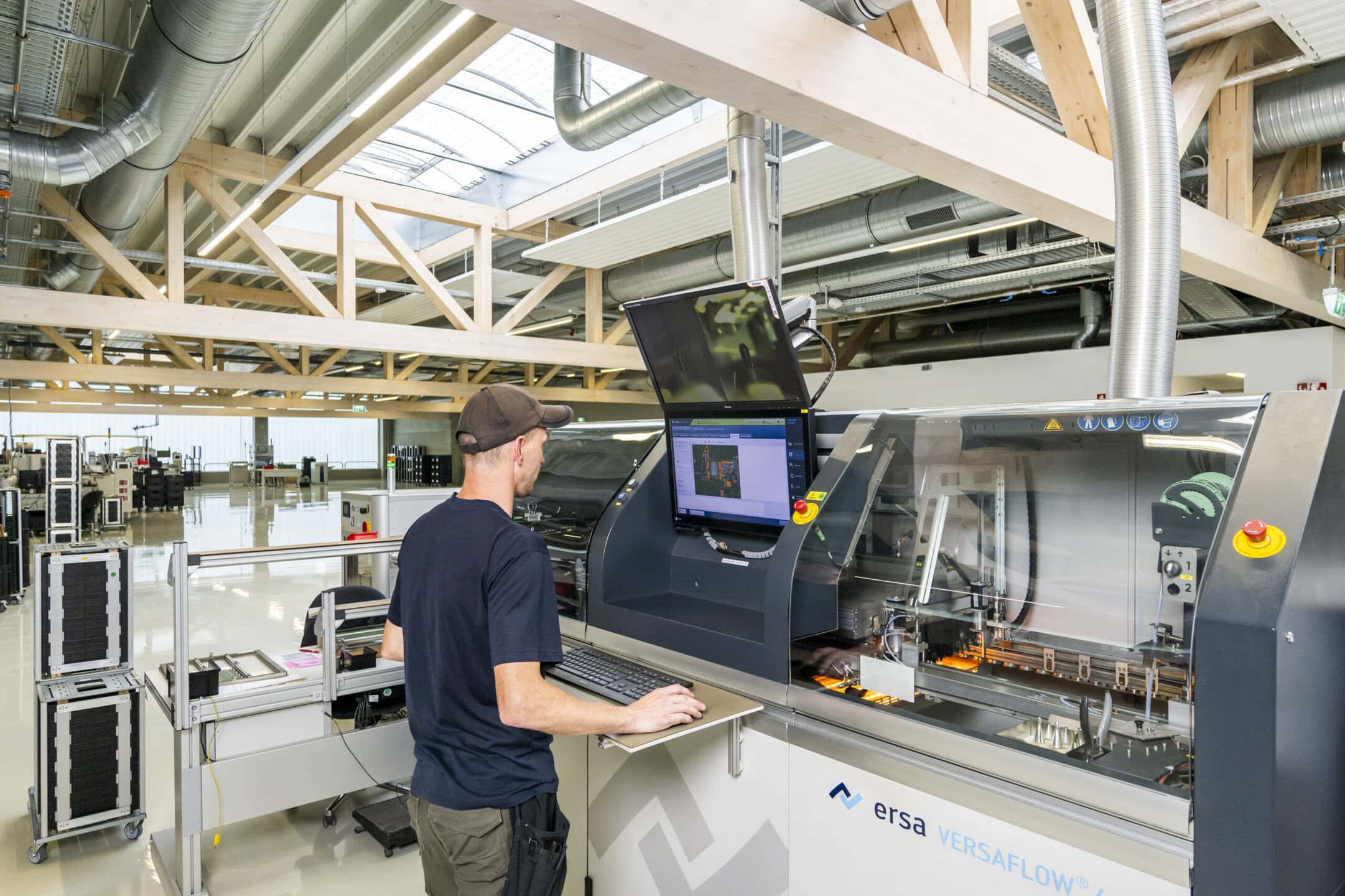
Assembly
Our assembly process includes the connection of electrical, electronic, electromechanical and mechanical assemblies to a level of integration that is customised to our customers’ needs. Painting and potting can be integrated into the assembly process. After assembly, our products undergo a final test, which may also include a high-voltage test, depending on requirements.
Traceability
Traceability is crucial in modern manufacturing. It allows us to fully trace all process steps and materials, ensuring compliance with quality standards, transparency and supply-chain security. Our traceability system ensures that our processes are carried out correctly and in the correct order.
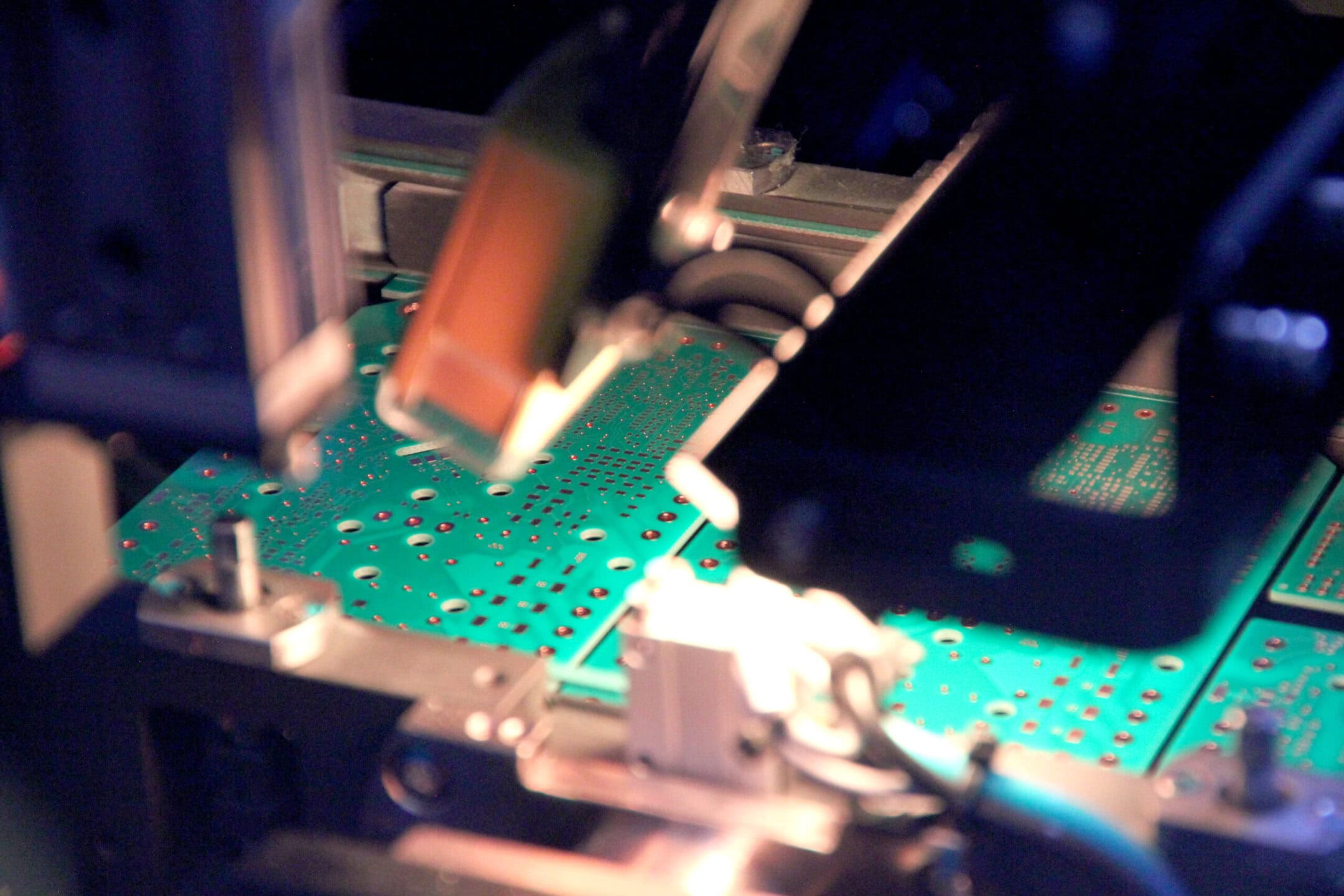