Company
Quality
For us, quality is the sum of all criteria by which our customers determine their satisfaction with us, our services and our products. For us, quality also entails responsibility towards our employees and our environment.
Sustainability
Sustainability is a central component of our company. We focus on environmentally friendly production processes, reduce our CO2 emissions and promote the use of renewable energies. We also attach great importance to the responsible procurement of raw materials, the minimisation of waste through recycling and the efficient use of resources.
Our sustainability strategy aims to assume long-term economic, ecological and social responsibility in order to make a positive contribution to the environment and society.
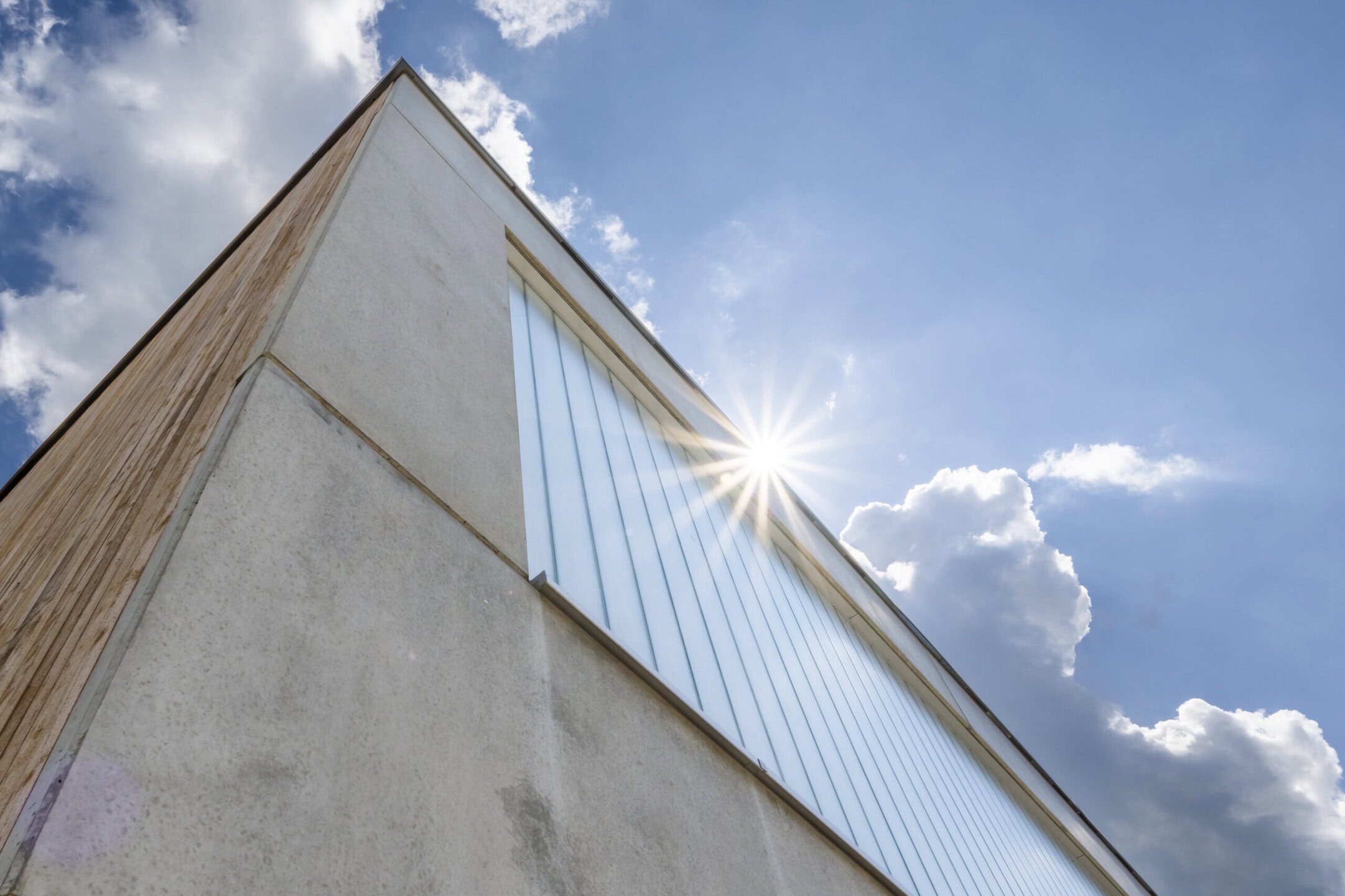
Company History
2025
New home for development department
In the heart of the historic old building, where electronics were once assembled, ultra-modern workstations are being created for the development department.
2025
Market launch of a new charger
Start of production of an ultra-compact, onboard charger (19.5 × 15.7 × 8.1 cm) with 2 kW output, protection class IP54 and active cooling.
2024
Expansion of production capacities
Electronics production moves into the new hall. Installation and integration of a vacuum potting system. Start of production for a compact onboard charger with 0.5 kW power, protection class IP54 and passive cooling.
2023
Expansion of the production area
Construction and completion of a 1,800-m² production hall for electronics production at the site with extensive use of renewable raw materials and utilisation of geothermal energy for cooling and heating the building and various processes.
2022
Introduction of new marking technologies
Commissioning of a laser-marking system for 100% labelling of all assemblies, thus creating the basis for end-to-end traceability.
2020
Further development of charger production
Start of production of onboard chargers in the 1 kW and 1.8 kW power classes with protection class IP54.
2018
Flying-probe commissioning
Commissioning of the automatic electrical test procedure for in-circuit testing of the top and bottom of the manufactured assemblies.
Supplemented by selective soldering system
Parameters for each solder joint can be individually programmed and monitored. Flux quantities and soldering times are selectively controlled. Higher quality and better reproducibility of soldering results.
2013
Move into the extension for warehouse and office
Extension doubles the floor space to 2400 m². Construction of a fully air-conditioned production room with positive pressure.
2008
Commissioning of the first potting line
Fully automatic potting lines for two-component potting under constant conditions (material preparation under vacuum, with temperature control and agitator) ensures consistently high potting quality.
2006
Introduction of RoHS-compliant production
Conversion of all soldering processes to lead-free solder.
2003
Certification according to DIN EN ISO 9001:2000
Introduction of a quality-management system for continuous improvement and further development. Certification according to DIN EN ISO 9001:2008.
2002
Automation of THT and SMT assembly
Universal THT assembly line for axially and radially taped components and an SMT production island with two high-performance SMT lines are integrated into the production process.
2001
Relocation to new company building
The company moves into new premises with a usable area of 1200 m².
1997
Start of series production of the first TCE motor controller
Controls with one- to four-quadrant control and outputs up to 8 kW developed and successfully established on the market. This is the cornerstone of the second important business segment.
1994
Series production of the first own charger, the GIM®60
The performance spectrum ranges from ‘classic hourly chargers’ with 1.5 A charging current at up to 12 V nominal voltage to fast chargers that can charge battery packs with 36 V nominal voltage and up to 35 A charging current. Integrated microcontrollers in each charger make it possible to react flexibly to customer change requests and adapt the devices to new market requirements.
1992
Foundation of TCE in Frankenberg
Start of production of assemblies for chargers for well-known power tool manufacturers. Start of development of TCE´s own charging technology.