Unternehmen
Qualität
Qualität ist für uns die Summe aller Kriterien, an denen unsere Kunden ihre Zufriedenheit mit uns, unseren Dienstleistungen und unseren Produkten bestimmen. Qualität bedeutet für uns aber auch Verantwortung unseren Mitarbeitern und unserer Umwelt gegenüber.
Nachhaltigkeit
Nachhaltigkeit ist ein zentraler Bestandteil unseres Unternehmens. Wir setzen auf umweltfreundliche Produktionsprozesse, reduzieren unseren CO2-Ausstoß und fördern den Einsatz erneuerbarer Energien. Zudem legen wir großen Wert auf die verantwortungsvolle Beschaffung von Rohstoffen und die Minimierung von Abfällen durch Recycling und effiziente Ressourcennutzung.
Unsere Nachhaltigkeitsstrategie zielt darauf ab, langfristig ökonomische, ökologische und soziale Verantwortung zu übernehmen, um einen positiven Beitrag für die Umwelt und die Gesellschaft zu leisten.
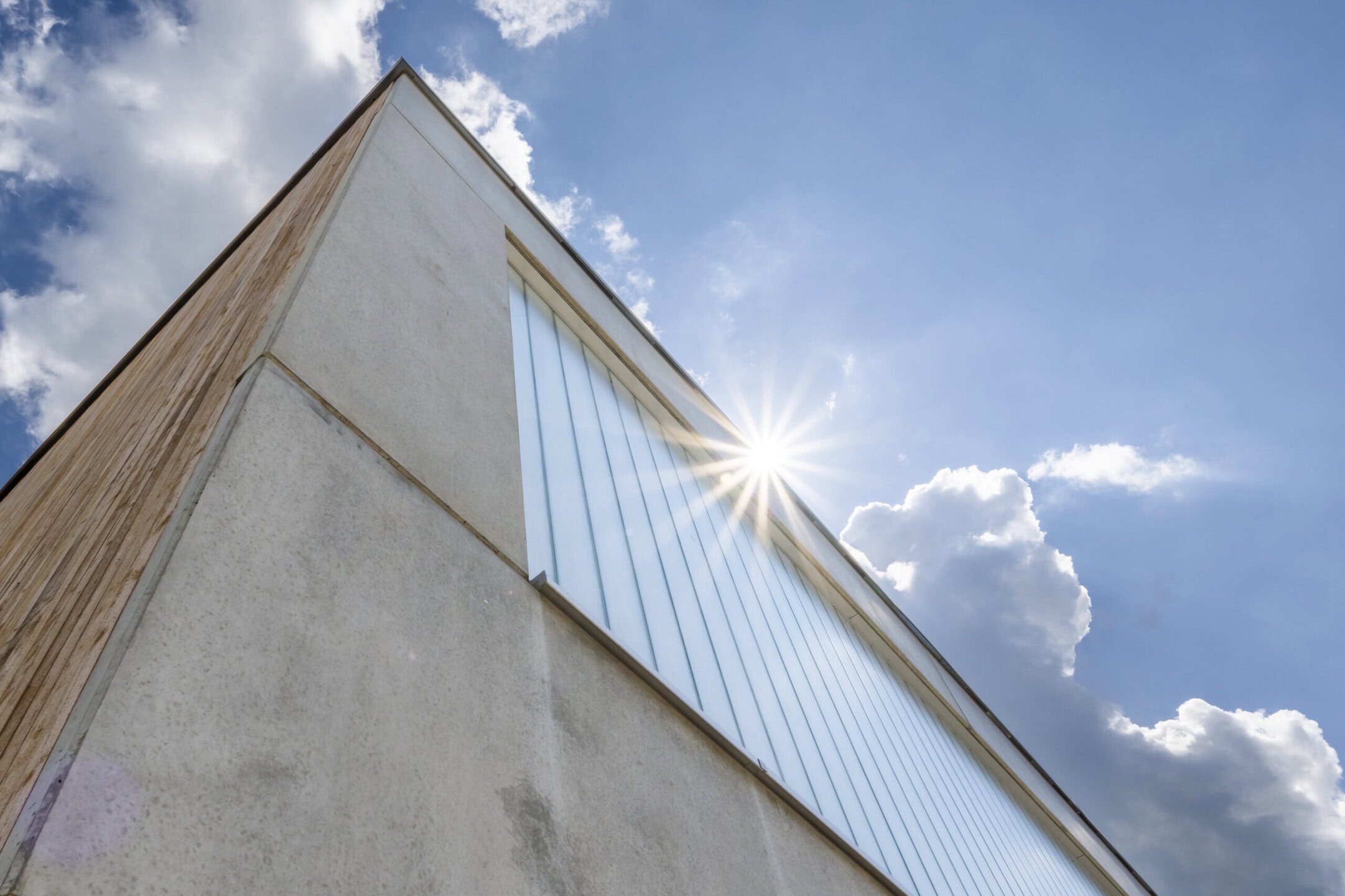
Geschichte
2025
Neues Domizil für Entwicklungsabteilung
Im Herzen des historischen Altbaus, dort wo ehemals Elektroniken bestückt wurden, entstehen hochmoderne Arbeitsplätze für die Entwicklungsabteilung.
2025
Markteinführung eines neuen Ladegeräts
Produktionsstart für ein ultrakompaktes On-Board-Ladegerät (19,5 x 15,7 x 8,1 cm) mit 2 kW Leistung, Schutzklasse IP54 und aktiver Kühlung.
2024
Erweiterung der Produktionskapazitäten
Einzug der Elektronikfertigung in die neue Halle. Installation und Integration einer Vakuum-Vergussanlage. Produktionsstart für ein kompaktes On-Board-Ladegerät mit 0,5 kW Leistung, Schutzklasse IP54 und passiver Kühlung.
2023
Erweiterung der Produktionsfläche
Bau und Fertigstellung einer 1.800 m² großen Produktionshalle für die Elektronikfertigung am Standort bei umfassendem Einsatz nachwachsender Rochstoffe und Nutzung von Geothermie zur Kühlung und Heizung des Gebäudes bzw. verschiedener Prozesse.
2022
Einführung neuer Markierungstechnologien
Inbetriebnahme einer Lasermarkieranlage zur 100%igen Kennzeichnung aller Baugruppen und damit Schaffung der Grundlage für eine durchgängige Traceability.
2020
Weiterentwicklung der Ladegerätproduktion
Produktionsstart von On-Board-Ladegeräten in den Leistungsklassen 1 kW und 1,8 kW mit der Schutzklasse IP54.
2018
Inbetriebnahme Flying Probe
Inbetriebnahme des automatischen elektrischen Testverfahrens zur In-Circuit-Prüfung der Ober- und Unterseite der gefertigten Baugruppen.
Ergänzung durch Selektivlötanlage
Parameter für jede Lötstelle können einzeln programmiert und überwacht werden. Flussmittelmenge und die Lötzeit werden selektiv gesteuert. Höhere Qualität und bessere Reproduzierbarkeit der Lötergebnisse.
2013
Bezug des Erweiterungsbaus für Lager und Büro
Anbau verdoppelt die Nutzfläche auf 2400 m². Errichtung eines vollklimatisierten Produktionsraums mit Überdruck.
2008
Inbetriebnahme erste Vergusslinie
Vollautomatischen Vergusslinien für Zwei-Komponenten-Verguss unter stets konstanten Bedingungen (Materialaufbereitung unter Vakuum, mit Temperaturregelung und Rührwerk) sichert durchgehend hohe Vergussqualität.
2006
Einführung RoHS-konformer Fertigung
Umstellung aller Lötprozesse auf bleifreies Lot.
2003
Zertifizierung nach DIN EN ISO 9001:2000
Einführung eines Qualitätsmanagementsystems zur ständigen Verbesserung und Weiterentwicklung. Zertifizierung nach DIN EN ISO 9001:2008.
2002
Automatisierung der THT- und SMT-Bestückung
Universelle THT-Bestückungslinie für axial und radial gegurtete Bauteile sowie eine SMT-Fertigungsinsel mit zwei leistungsstarken SMT-Linien sind im Produktionsprozess integriert.
2001
Umzug in neues Firmengebäude
Neues Betriebsgebäude mit einer Nutzfläche von 1200 m² bezogen.
1997
Serienstart der ersten TCE-Motorsteuerung
Steuerungen mit Ein- bis Vier-Quadranten-Regelung und Leistungen bis 8 kW entwickelt und erfolgreich am Markt etabliert. Das ist der Grundstein das zweites wichtige Geschäftsfeld.
1994
Serienproduktion des ersten eigenen Ladegeräts GIM®60
Das Leistungsspektrum reicht von „klassischen Stundenladern“ mit 1,5 A Ladestrom bei bis zu 12 V Nennspannung bis hin zu Schnellladegeräten, die Akkupacks mit 36 V Nennspannung und mit bis zu 35 A laden können. Integrierte Microcontroller in jedem Ladegerät erlauben es, flexibel auf die Änderungswünsche der Kunden zu reagieren und die Geräte an neue Anforderungen des Marktes anzupassen.
1992
Gründung von TCE in Frankenberg
Beginn der Fertigung von Baugruppen für Ladegeräte namhafter Elektrowerkzeughersteller. Start der Entwicklung eigener Ladetechnik.